A Guide to Low-Slope Roofs
- Trident Property Management - SWO
- Jan 19, 2022
- 5 min read
F
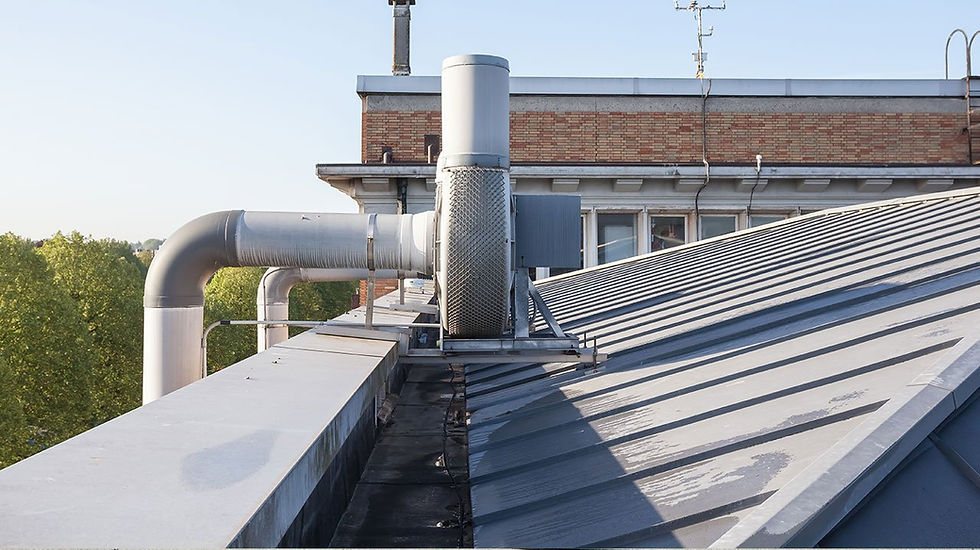
ew building components are more critical to the overall functionality of a property than the roof system. The roof controls water penetration, air and heat flow, vapour diffusion, as well as overall protection.
Weather and exposure to UV radiation from sunlight are the main factors that cause roofs to age. In Canada, we face a particularly harsh climate with dramatic temperature fluctuations. This weather can in turn speed up the degradation of a roof.
Bi-annual inspections and maintenance are recommended to detect and prevent minor issues from becoming major problems. This can be as simple as cleaning and removing any debris from the roof and clearing roof drains. Larger issues, such as blistering, cracks, or tears should be addressed immediately.
Qualified roofing experts can detect hidden issues, such as moisture retention through the use of infrared thermography and capacitance scanners. Test cuts can also be used to detect the presence of moisture. However, this involves penetrating the roof membrane.
Repair, or replacement of a roof system is an unfortunate reality for virtually every property owner. It can be one of the most expensive replacement items, and if neglected, can lead to a host of other building issues.
Understanding the basic components and types of roofs can save property owners money in the long run.
1) Primary Components of a Low Slope Roof
For the purpose of this article, we are discussing low-slope roofs, commonly found in commercial applications:
Roof Deck
This is the support structure responsible for transferring the load of the roof. Typical construction consists of metal, wood, or concrete.
Vapour Barrier

This component is responsible for limiting the amount of moisture that transfers from inside the building to the roof system.
Roof Insulation
The insulation is responsible for heat flow into and out of the building. The degree of insulation is typically measured by its resistance to heat flow, or R-value.
Roof Membrane
This is the top layer responsible for protecting the building from weather, UV radiation and any physical damage. There are a number of different roof membranes to choose from, dependent on the application, budget, climate, or personal preference of the building owner.
2) Commonly Used Low-Slope Roof Systems
(i) Built-Up Roofs (BUR)
This method involves building up multiple layers of reinforcing fabrics between layers of heated bitumen, or asphalt. The top layer consists of a final coat of bitumen into which gravel, or a coating is applied. As the bitumen cools it solidifies into a single solid structure. This structure is fairly rigid and inflexible and can become brittle in extreme cold temperatures.
Advantages:
- Multiple layers of protection
- Holds up well against physical abuse
- Long life if properly installed
Disadvantages:
- Expensive to repair
- Requires qualified contractor to install
- Higher labour costs
(ii) Modified Bitumen
This typically involves two layers of membrane. Instead of reinforcing with fabrics, asphalt is combined with rubber polymers into a thick roll. The rubber allows for flexibility and stronger performance in colder climates than BUR systems.
Rolls are adhered to the roof system either by mopping them in asphalt, or torching them with an open flame. This creates the obvious risk of fire during application. More recent applications allow for an adhesive to connect adjacent rolls.
Advantages:
- Improved flexibility compared to BUR
- Two layers of protection
- Longer lifespan than BUR systems
Disadvantages:
- Higher cost than other systems
- Rolls create numerous seams
- Expensive to repair
(iii) EPDM

EPDM is a synthetic rubber membrane installed as a single ply and comes in various colours and thicknesses. Thicker membranes offer better resistance to physical damage. Rolls of EPDM can range in width from 5 to 50 feet, which allows for fewer seams and quicker installation. Rolls are attached to one another using adhesive tape. The EPDM membrane is considered one of the most popular for commercial application throughout North America.
Advantages:
- High resistance to UV and weather
- Inexpensive to repair
- Lower labour cost to install
Disadvantages:
- Fewer layers are less resistant to puncture
- Difficult to install around rooftop units
(iv) PVC
PVC has been used as a roofing membrane since the 1960’s and offer a white, or grey application.
PVC roofs are more common in locations that allow for the roof to be visible from street level (ie. dome-shaped roofs). The colour options allow for an aesthetic component for those willing to pay for it.
One of the major concerns with using PVC as a roofing membrane is that the additives which make it pliable can leach out overtime, making the membrane brittle and inflexible. This is accelerated by prolonged exposure to sunlight, water, and other types of plastics.
Advantages:
- Easily and inexpensively repaired
- White membrane offers energy savings
- Logos can be incorporated into the roof
Disadvantages:
- High pollution from manufacturing
- Generally more expensive vs. other options
- Membrane loses flexibility over time
(v) TPO
This product was designed to combine the positive attributes of EPDM and PVC. The properties of TPO allow for the seams to be hot air fused together, along with a flexible membrane which is resistant to cold temperatures. This product comes in white, grey, and tan. The lighter colours allow for an energy saving component as well.
TPO roofs have grown in popularity in recent years, particularly for their ability to recover an existing membrane, where full roof replacement may not be an option.
Advantages:
- Easily and inexpensively repaired
- White membrane offers energy savings
- Logos can be incorporated into the roof
Disadvantages:
- Thinner sheets more prone to puncture
- Newer product with unproven lifecycle
Not all roofs require a full replacement. In the right situation a roof restoration may be a preferred option to extend the roof’s lifespan. This typically involves the application of some coating to the existing membrane, and addressing any damaged areas. Where applicable, this can dramatically reduce the cost to the property owner, compared with a full roof replacement.
Roof recovering offers another alternative to full replacement. This generally involves applying a new membrane over the existing structure. In some cases, the existing membrane can be left intact. However, if the membrane is too damaged it will need to be removed and a new membrane applied. Recovering provides for a cheaper alternative to full replacement as the rest of the roof structure (deck, vapour barrier and insulation) remains intact.
Full replacement generally requires removing the entire assembly right down to the roof deck, or in some cases to the structural supports if the deck is too damaged. While this is the most expensive option, it does generally provide for the best warranty protection of the 3 options.
The cost of each of these options will vary based on the extent of any damage and the product being used. When choosing the appropriate application there are a number of factors to consider: Longevity and life expectancy of a product; ongoing maintenance requirements; initial, as well as ongoing maintenance costs; warranty being offered; and resistance to roof traffic and physical abuse, to name a few.
Consulting with a qualified roofing expert and understanding the options available can help save a property owner time and money.
Comments